Welcome to the world of polyurea, a versatile and high-performance coating revolutionizing various industries across Canada. In this blog post, we will dive deep into the fundamentals of polyurea, its numerous applications, and the advantages it offers to businesses in the Canadian market. So, let’s embark on this informative journey together and discover how polyurea can enhance your projects and operations.
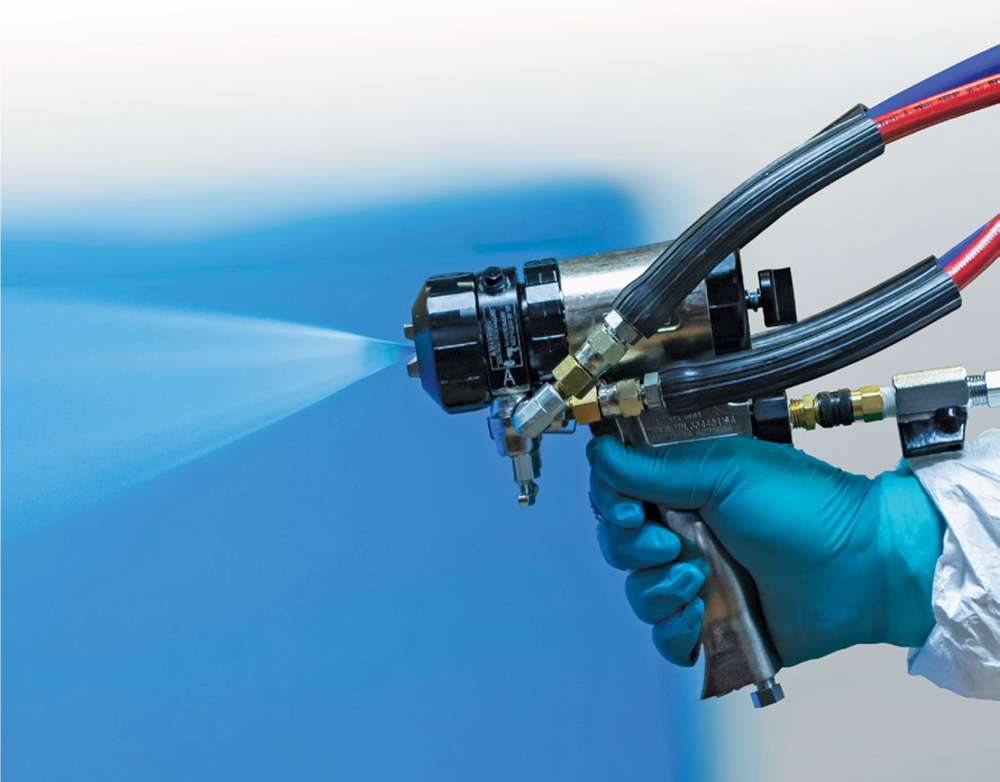
What is Polyurea?
Polyurea is a cutting-edge, two-component, spray-applied elastomer that combines the properties of both plastics and rubbers. It is created by the reaction of an isocyanate component with an amine-terminated resin blend. This innovative material boasts exceptional durability, flexibility, and chemical resistance, making it a popular choice for a wide range of industries, including construction, automotive, marine, and more.
Why Polyurea is Gaining Popularity in Canada
Polyurea’s growing popularity in Canada can be attributed to several factors that set it apart from traditional coating materials. Here are some of the key reasons why Canadian industries are increasingly adopting polyurea:
1. Remarkable Durability and Strength
Polyurea coatings are known for their exceptional durability and ability to withstand extreme wear and tear. This makes them an ideal choice for applications that require long-lasting protection, such as heavy machinery, industrial flooring, and infrastructure projects.
2. Quick Cure Time
One of the most significant advantages of polyurea is its rapid cure time. The material can set within seconds and achieve full cure within 24 hours, allowing for minimal downtime during the application process. This is particularly beneficial for industries that cannot afford extended downtime, such as manufacturing plants and transportation facilities.
3. Extreme Temperature Resistance
Canada is known for its harsh weather conditions, with temperatures often dipping well below freezing during winter. Polyurea’s ability to perform exceptionally well in extreme temperatures makes it an attractive option for Canadian industries that require robust protection against the elements.
4. Waterproof and Chemical Resistant
Polyurea coatings provide excellent waterproofing and chemical resistance, making them suitable for applications where exposure to water, chemicals, or corrosive substances is a concern. This includes industries such as oil and gas, wastewater treatment, and marine applications.
5. Flexibility and Elongation
Polyurea’s inherent flexibility allows it to expand and contract with the substrate, making it ideal for applications where movement or stress is expected. This characteristic makes it popular for bridge deck coatings, parking garages, and other structures that experience regular movement or expansion.
Applications of Polyurea in Canadian Industries
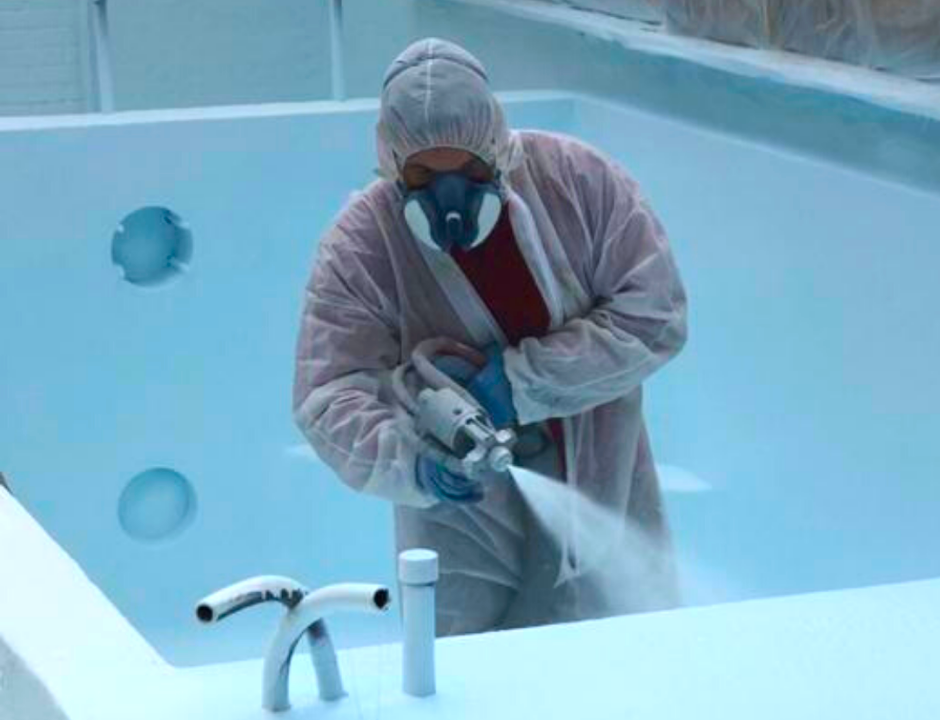
The versatility of polyurea allows it to be used across a wide range of industries in Canada. Here are some of the most common applications:
1. Construction
Polyurea coatings can protect concrete, steel, and wood surfaces in various construction projects, such as commercial buildings, residential properties, and infrastructure projects. Examples include waterproofing foundations, sealing expansion joints, and providing durable flooring solutions.
2. Automotive and Transportation
In the automotive and transportation sectors, polyurea coatings are used to protect vehicles, equipment, and infrastructure from wear, corrosion, and the elements. Applications include truck bed liners, undercoating for vehicles, and protective coatings for transportation infrastructure such as bridges and railings.
3. Oil and Gas
Polyurea is widely used in the oil and gas industry to protect pipelines, storage tanks, and other equipment from corrosion, chemicals, and environmental damage. The material’s ability to withstand extreme temperatures and harsh conditions makes it an ideal choice for this demanding industry.
4. Marine
The marine industry benefits from polyurea’s waterproofing and chemical resistance properties, making it an excellent choice for protecting boats, ships, and other marine structures from corrosion and damage caused by exposure to water and harsh chemicals.
5. Agricultural
Polyurea coatings can be used to protect agricultural equipment, buildings, and storage facilities from wear, corrosion, and environmental damage. Applications include silo linings, equipment protection, and livestock facility flooring.
Canadian Polyurea: Your Trusted Partner for Quality Polyurea Solutions
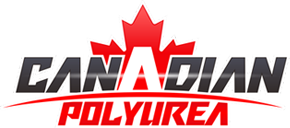
At Canadian Polyurea, we pride ourselves on providing high-quality polyurea products and services to meet the diverse needs of our clients across Canada. Our experienced team is committed to helping you find the ideal polyurea solution for your project, ensuring you receive the best value and performance possible.
Whether you require polyurea for a small residential project or a large-scale industrial application, Canadian Polyurea has the expertise, products, and support to help you succeed. Contact us today to learn more about how polyurea can enhance your projects and operations.